As lockdowns and restrictions continue, job training and opportunities lessen. In April 2020 it was reported that there was an 80% reduction for apprenticeship starts in the UK.
The focus has become heavily reliant on the theory and learning of the training, rather than the physical practice for many apprenticeships.
Recruitment training is a crucial time when it comes to careers and professions. Managers and leaders use this method to obtain order and hire qualified members that will impact their companies positively.
Many apprentices and employees have taken on the task of learning and working remotely.

Jordan Green, a mechanical engineer apprentice, said: “Covid-19 has made it so much harder to get on with work. I don’t feel like I’m learning the amount that I would have if I was in college/the professional atmosphere”.
Like many other apprenticeships, mechanical engineering is a very practical-sided job. Although the theory is important, experience and practice are crucial. This job is a necessity for our society to continue and withstand the basis and make advancement in transformation.
However, as restrictions prevent learning, the undeniable assumption of gen z workers being qualified enough in the profession in the future is yet to be confirmed.
Mr Green said, “I’m not as confident as I think I would have been if this virus didn’t exist. I need more time in the practical area because I honestly can’t do it on theory alone”
“It worries me knowing that soon I will be put into the real world of mechanical engineering and have no idea of what I am doing because all I learnt was the theory from the comfort of my bed”.
Many apprenticeships that require practical work are in danger of having untrained, hesitant employees for the future of their industry due to the Coronavirus.
Learning has continued in virtual classrooms, but is that enough to ensure the future of our businesses and companies?
It is still unclear and yet to be distinguished the long-term effects that covid-19 has had on apprenticeships.
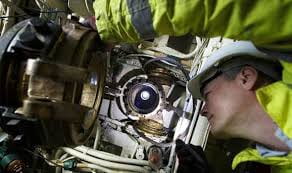
Christopher May, a mechanical engineer employee of Babcock for over 30 years, shared “This job isn’t easy. We work with toxic substances, materials that are extremely dangerous and powerful machinery. The environment is open to explosions, failures, malfunctions and fires- to work here it is vital that you know what you are doing”.
A private report of mechanical employees in Babcock showed that over 85% of the workers there were concerned about the dangerous environment these new apprentices would be put in, without having the proper training they would otherwise have under normal circumstances.